Padsons Cotton Seed Delinting Plant
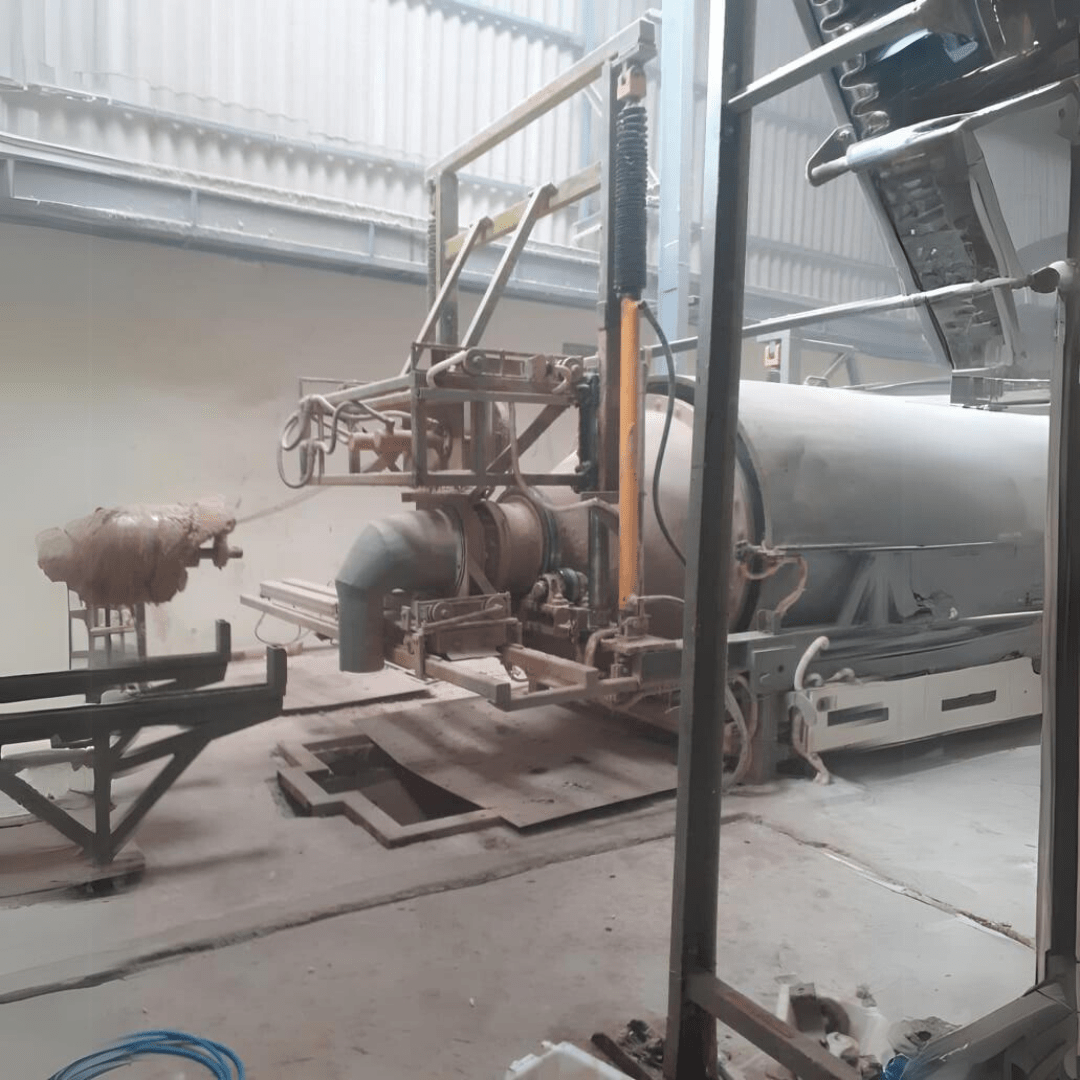
Padsons Cotton Seed Delinting Plant
Business Type | Manufacturer, Exporter, Supplier |
Type | Turnkey Plant |
Certification | CE Certified, ISO 9001:2008 |
Application | Padsons Cotton Seed Delinting Plant |
Power Requirement | 110.50 HP (83 KW) Seed Grader |
We are the best Eco friendly Cotton Seed Delinting Plant Manufacturer in Maharashtra. De-linting of cotton seed is the process of removal of fuzz (lint) from fuzzy cotton seeds. this seed delinting process is essential to have ease in cleaning, seed treatment, and high germination values; to achieve economical planting (because lint free seed grows much faster).
Salient Features of PADSONS AHCL Cotton Delinting plant:
- Complete automatic and operational friendly.
- Available in different batch sizes i.e. 75 /100/200 Kg per batch.
- Number of batches 3 per hour.
- Almost Pollution free.
- No need of ETP as no effluent is generated during the process. De-linting is AHCL gas base.
- Process is totally dry; No use of water during the process.
- Disposal of process waste i.e. linter powder is possible.
- So far 14 + customer bases across the country.
Consumption of various gases:
- AHCL: 1 Kg gas per 100 Kg of seed for the AHCL Cotton Delinting plant process.
- Ammonia: 400 to 500 gm per 100 Kg of seed for the neutralization.
- Nitrogen: 2-3 kg per day for general cleaning of gas manifold at end of shift.
Process sequence:
- Weighing of the seed lot on electronic weighing machine. The weight will be displayed on electronic display screen.
- The seed is then loaded to incline conveyor, where the seed is conveyed to next unit called Pre-conditioning. The incline conveyer conveys the seed by cleated belt. In the process of pre-conditioning the dust and loose lint is removed from the seed. The dust is collected in bottom hopper.
- The seed is then unloaded to charging trolley by opening the front gate of pre conditioning chamber with the help of switch provided on control panel pendant. The trolley moves forward and charge the seed to de-linting chamber (Reaction chamber)
- The de-linting chamber (Reaction chamber): where HCL gas is injected at predetermined rate. Here the decision of amount of gas to be injected in de-linting chamber is taken by PLC. Dosing and temperature of gas in chamber depends on size of batch. All other operations of plant are performed through control panel. HCL gas converts the fuss in powder form.
- Buffing: In this process the small portion of the lint attached to the seed is removed by continuous buffing action of the seeds against the rotating sieve drum. The separated lint powder freely falls down into the lint pit and taken out of the plant by screw conveyor.
- Neutralizing: The de-linted seed is of acidic in nature and hence it has to be neutralized. The de-linted seed bulk is then passed to three stage neutralizer chamber where required quantity of un-hydrous ammonia is passed to neutralize the seed. Neutralization is the last process in gas de-linting, after which, the seed is taken for further processing like grading & cleaning after checking the desired PH level.